Let’s get it together. Whether you're working in construction, automotive repair, aerospace, or fabrication, Global Industrial is your one-stop solution for welding equipment. With cutting-edge technology, welding accessories, safety gear, and expert guidance, this buyer’s guide will ensure you’re well-equipped for any metal welding project. Let’s start with the basics…
When to Choose Welding
At its core, welding creates a permanent bond between metals that can withstand extreme conditions. Whether you're creating structural components, fixing machinery, or building metal products, welding offers unparalleled strength compared to other joining methods like brazing and soldering. There are some clear advantages to welding: strong joints, heat resistance, and the versatility to be applied to both thin and thick materials. But like any process, there are some clear disadvantages as well. Welding can cause thermal distortion and residual stress in the joints which may require post-treatment. Welding is generally unsuitable for joining dissimilar metals. Also visible welding beads can make it less cosmetically pleasing for applications where aesthetics are a priority. These are all key factors when deciding what types of welding are the right processes for the job.
Welding is integral to many industries, from manufacturing to transportation and construction. Key applications include:
- Robotic Assemblies: Precision welding for manufacturing plants.
- Building Structures: Joining steel and other metals for constructing buildings, bridges, and other large structures.
- Automotive and Aircraft: Fabricating components for vehicles and airplanes.
- Pipelines: Welding sections of pipelines together for transporting oil, gas, and water.
- Repair Shops: Fixing machinery, automotive parts, and other metal components.
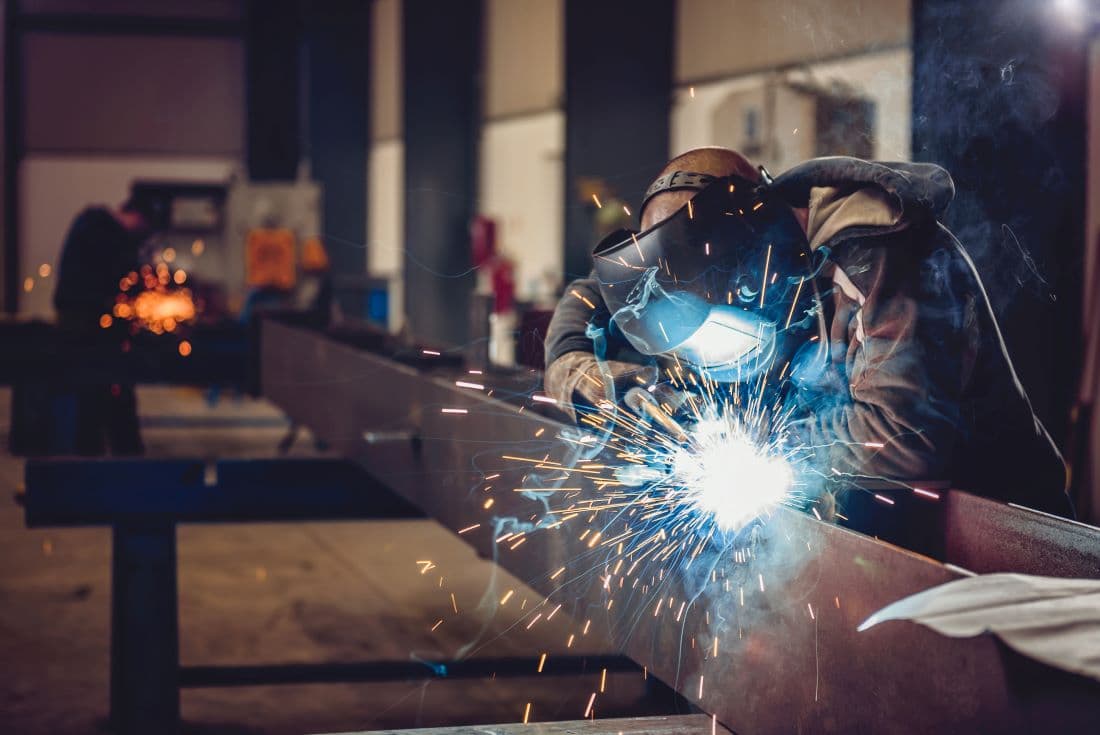
Welding vs. Brazing vs. Soldering
Although welding, brazing, and soldering all involve joining metals, they differ in terms of temperature and material behavior.
- Welding: Involves melting the base material and using a filler. It is suitable for high-strength applications and a wide range of materials.
- Brazing: Uses a filler material but does not melt the base metals. It is better for joining dissimilar metals and requires lower temperatures.
- Soldering: Operates at even lower temperatures, bonding materials without altering the base metal’s properties, making it suitable for electrical and plumbing applications.
The method you choose depends on your material, desired strength, and application. For instance, welding is ideal for structural work, while soldering is better for delicate electrical connections.
Are You a Beginner or an Experienced Welder?
Your skill level plays a key role in selecting the right welding method.
- Beginner: MIG (Metal Inert Gas) welding is often considered the easiest to learn, offering flexibility for various metals like mild steel and aluminum.
- Experienced: TIG (Tungsten Inert Gas) welding is preferred by professionals for its precision and ability to weld metals like aluminum and stainless steel.
The Four Main Types of Welding Processes
- Gas Metal Arc Welding (GMAW/MIG)
MIG welding uses an electrical supply to fuse the base metal with a consumable electrode filler. It works on materials like mild steel, low-alloy steel, stainless steel, and aluminum. MIG welding is popular for its ease of use, making it an excellent option for beginners and medium-duty industrial applications. - Gas Tungsten Arc Welding (GTAW/TIG)
TIG welding employs a non-consumable tungsten electrode, ideal for more precise work. It’s commonly used for stainless steel, aluminum, and other exotic metals. Though more challenging to master, TIG welding offers high-quality results and is a go-to for experienced welders. - Shielded Metal Arc Welding (SMAW)
Commonly known as stick welding, SMAW involves creating an electric arc between a consumable electrode and the workpiece. Using an arc welder is highly versatile, perfect for stainless steel welding, carbon steel welding, and cast iron welding., and is ideal for both indoor and outdoor applications, especially in construction. - Flux-Cored Arc Welding (FCAW)
FCAW, or dual shield welding, is similar to MIG welding but uses a flux core in the wire, allowing it to work well on thicker materials and surfaces that may not be pristine. This makes it a great choice for heavy-duty applications and outdoor work.
Factors to Consider When Buying a Welder
Selecting the right welder depends on the specific needs of your projects. Consider these essential factors:
- Material Type - The material you plan to weld (e.g., steel, aluminum, or stainless steel) will determine the welding process and machine type. MIG and stick welders are good for steel, while TIG is preferred for aluminum and stainless steel.
- Welding Capacity - The thickness of the material you’ll be working with matters. For example, a 140-amp machine can weld up to 1/4 inch steel, while a 250-amp machine can handle up to 1/2 inch. Make sure your machine’s power matches your material needs.
- Primary Power Requirements - Welding machines can use either alternating current (AC) or direct current (DC), and your power source will affect your welder's capacity. Standard household outlets support smaller, less powerful machines, while industrial welders may require 240V or more.
- Portability, Size, and Weight - For jobs that require mobility, opt for portable welders. A lighter, more compact machine is easier to transport, but it may come with trade-offs in power and duty cycle.
- Welding Output and Duty Cycle - The duty cycle is the amount of time the machine can weld without overheating. For continuous, industrial-scale welding, look for a higher duty cycle.
- Electrode Selection - Different electrodes are suited for various metals and applications. Be sure to select the appropriate type for your project, particularly if you’re using a stick or TIG welder.
- Shielding Gas Requirements - Some welders, like MIG and TIG, require shielding gas to protect the weld area from contaminants. Ensure you have the correct gas (e.g., argon, carbon dioxide) for your welding setup.
- Safety Features - Welding involves high temperatures, electricity, and gas, making safety paramount. Look for machines with automatic shutoff features, overcurrent protection, and other safety mechanisms.
- Accessories - Invest in the right accessories for your welding setup. Essential items include welding tables, clamps, and angle grinders. The proper arc welding supplies are essential to a job well done. Don’t forget protective equipment, such as helmets, gloves, and barriers, to ensure safety during the welding process.
Welding Product Categories
At Global Industrial, we offer a wide range of welding products to suit various applications:
Choosing the right welding equipment involves understanding your materials, power needs, skill level, and safety requirements. Whether you are a beginner or a professional welder, Global Industrial offers a comprehensive range of welding products, accessories, and safety equipment to help you get the job done efficiently and safely.
The information contained in this article is for informational, educational, and promotional purposes only and is based on information available as of the initial date of publication. It is the reader’s responsibility to ensure compliance with all applicable laws, rules, codes and regulations. If there is any question or doubt in regard to any element contained in this article, please consult a licensed professional. Under no circumstances will Global Industrial® be liable for any loss or damage caused by your reliance on this article.