GUARDING YOUR TOOLS: SMART JOBSITE STORAGE SOLUTIONS FOR YOUR VALUABLES
If you’re the kind of person who’s got a strategy for everything, except when it comes to jobsite storage, you’re not alone! Most people only think about storage when they need it and realize they don’t have it. But integrating a storage strategy directly into your game plan is a proactive way to avoid potential issues on the job before they arise.
Whether you need to increase floor space in your facilities, improve product mobility between stations, or just get organized once and for all, having a storage system in place can help optimize your workflow to positively impact productivity and project timelines across jobsites.
TYPES OF STORAGE
Because there are so many solutions available when it comes to jobsite storage, from handheld tool boxes to portable cabinets, to welder’s chests, it's important to assess your specific needs.
Heavy Duty Jobsite Storage Boxes
Welcome to the intersection of durability and security. Constructed from high-gauge metals, these sturdy, secure work boxes are designed to protect your gear from theft, damage, and weather, even in harsh conditions.
Tips:
- Check the specs. Do you need something that’s forklift accessible or compatible with crane lifts? If you might need to add a caster set in the future, look for jobsite storage chests with pre-drilled bolsters.
- Categorize by task. Even though our jobsite storage boxes are designed to keep everything within reach, sometimes, it’s easy to miss what’s right in front of you. Categorizing contents by task, or opting for models with built-in dividers, will make it even easier to reach for exactly what you need.
Portable Jobsite Storage Boxes and Chests
Portability is key, especially on dynamic jobsites. With a portable jobsite tool box or chest, your storage system will adapt to each location without skipping a beat, just like you.
Tips:
- Map out your workflow to decide what type of portability works for you. Many portable storage boxes are equipped with handles and wheels for easy transport between different areas of the jobsite.
- Consider the size and design. Compact options can provide ample storage space without taking up excessive room on the site, while a low profile jobsite box can mount to pick-up beds and trailers for convenient transport and storage.
Jobsite field offices are convenient mobile workspaces that allow you to stay organized and productive, wherever you are. And they’re built to resist corrosion and weather damage, so they’re built to last.
Tips:
- Choose a model with built-in sidewall bins to take your field office organization to the next level.
- Double check specifications on weight capacity when deciding which option will be best to meet your needs. If your haul changes a lot between sites, opt for a field office with anti-tip bars so everything stays exactly where you left it.
If your current storage solutions are no longer working for you, it might be time to customize the jobsite storage boxes you’ve already got. That's where accessories come in. Tailor your jobsite tool cabinet with shelving units, dividers, or hooks whenever a project calls for a change in your storage solutions. Make your jobsite workboxes portable by adding wheels or a crane lift kit, each of which boasts an impressive load capacity of 2,500 lbs. When storage solutions are one-size-fits-all, they tend to be more hassle than they’re worth. Ultimately, the best jobsite storage box is going to be the one that works best for you, so why not make it a custom fit?
BENEFITS
Efficiency
When an item or tool is out of place, there’s a decision to be made: do you spend the time to find it, or do you use the second best option because it’s closer and easier? Either way, time is wasted or work is compromised. Organization allows for faster work, easier stock assessment, and more accurate replenishment. When everything has its designated place, increased productivity and better workflow happen as a result.
Security
Theft and damage are potential hazards on any jobsite, but high-quality storage solutions like this upright jobsite cabinet have top notch security features like the WATCHMAN® IV Lock System, recessed lock housing for protection against theft, and a deadbolt style locking mechanism for added security. Minimize your risk with a storage system that’s secure.
Portability
As jobsites evolve and layouts change, portable storage solutions enable you to adapt to changing layouts and project phases. Whether you’re expanding your retail footprint, running a multi-location healthcare operation, updating your warehouse, or building up your community in the public sector - when you’re a pro on the go, portability matters.
Longevity
Investing in high-quality doesn’t just pay off in the long run, it gives you a return on your investment every day with the peace of mind that you’re prepared for the job ahead and that your tools and supplies are safely stored. Professional grade materials can meet the demands of harsh jobsite environments, and with regular maintenance, you’ll extend their lifespan even further, reducing the need for frequent replacements.
Accountability
When organization is part of your standard operating procedure, that becomes another channel of communication for a team that works in sync. Organization also fosters accountability among team members; with designated storage for tools and supplies, everyone becomes responsible for returning items to their rightful place, and in turn, teams have the confidence that when they reach for what they need, they’ll find it. That’s teamwork!
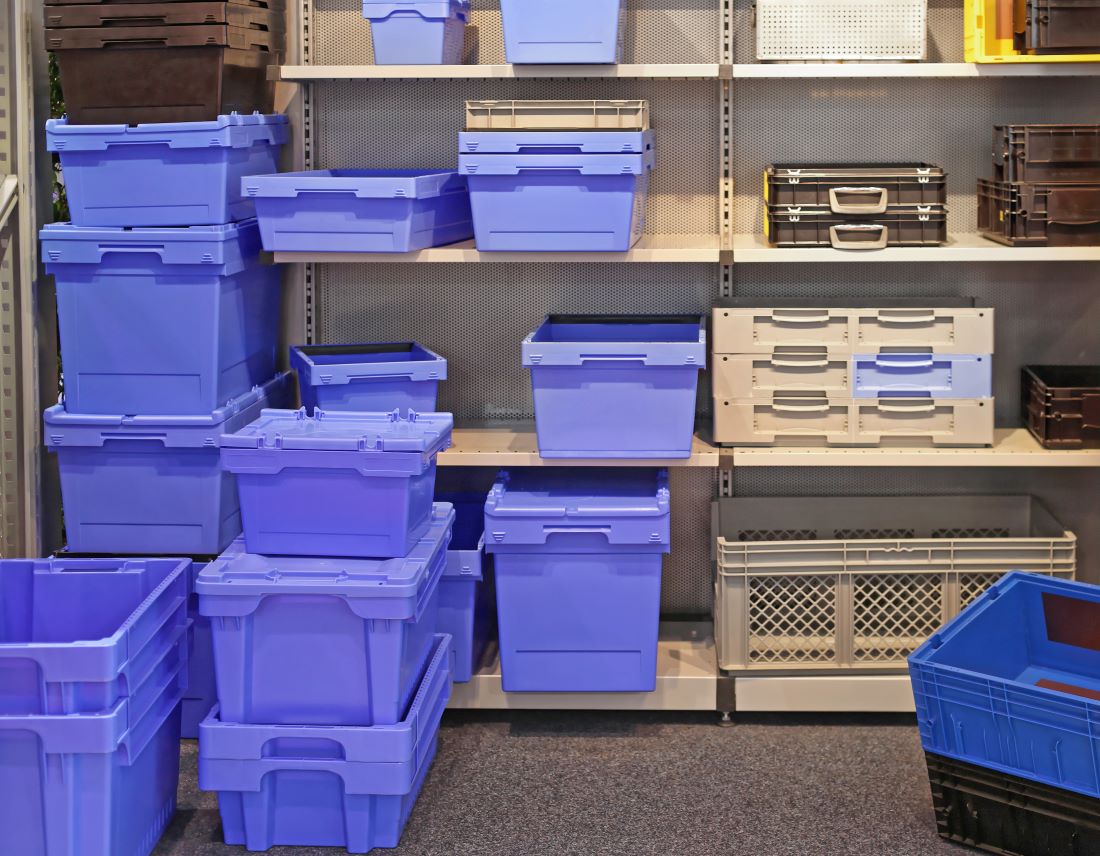
WHAT ARE YOU STORING?
To decide which jobsite storage solutions will work best for you, first consider what types of things you need to store.
Tools:
Your tools are one of your biggest investments - they’re what help you get the job done. So ensuring that those tools are always accessible, accounted for, and safely stored is a non-negotiable. Here’s how you can get the most out of your jobsite tool storage:
Tips:
- Add foam inserts to your jobsite tool box to help prevent damage during transport and storage. These inserts offer individualized compartments for each tool to limit unnecessary wear and breakage when they’re not being used.
- Include a steel tool tray to your current jobsite tool chest as a way to increase space and improve organization.
- Once you’ve gotten a handle on organization, ensure that your tools are always secure by choosing a jobsite storage box with robust locking mechanisms to deter theft.
Supplies:
From nails and screws to safety gear and cleaning supplies, if a jobsite calls for it, you need to have it (and you need to know where it is!).
Tips:
- Opt for clear or semi-transparent storage bins to scan contents at a glance. Minimize time spent searching while maximizing jobsite efficiency.
- Consider jobsite storage cabinets with adjustable shelving to cater to varying supply sizes for your changing needs.
- If what you’re storing requires a bit more than transparent bins can offer (like hazmat) make sure that whatever jobsite storage box you decide on meets EPA and UFC requirements.
Documents:
No matter what industry you’re in, disorganized documents are a recipe for disaster. But a well-organized command center with a foolproof filing system in place can help ensure that important paperwork is always at your fingertips. And if the computer crashes or the wifi is down, you’ll be the hero with hard copies!
Tips:
- Choose portable file boxes with built-in dividers to keep things like blueprints, permits, and contracts in order.
- Set clear organizational guidelines and protocols so that even when you’re hopping between jobsites, your organization strategies are still running smoothly.
- Implement a labeling system to categorize supplies, so teams can locate what they need, when they need it.
Effective jobsite storage is a strategic and often overlooked way to maximize efficiency, security, and workflow. By understanding what needs to be stored, selecting the right storage solutions, and continuing to assess and adapt your strategy as needs evolve, then you’re setting yourself up for success and leading a team that’s organized, prepared, and ready to work. Less mess means less stress. Don’t let poor storage planning stop your workflow.
To read more about some of the core features specific to Global Industrial’s suite of jobsite storage solutions, head to LinkedIn, check out our knowledge center, or get in touch with one of our pros today!
The information contained in this article is for informational, educational, and promotional purposes only and is based on information available as of the initial date of publication. It is the reader’s responsibility to ensure compliance with all applicable laws, rules, codes and regulations. If there is any question or doubt in regard to any element contained in this article, please consult a licensed professional. Under no circumstances will Global Industrial® be liable for any loss or damage caused by your reliance on this article.