The loading dock is the lynchpin of any warehouse operation, and is most likely the busiest part of your facility. It’s the gateway for goods to come in and out of your business, and so it’s essential to ensure this is both a safe and well-oiled machine. Sadly, loading dock safety is often overlooked and that’s when accidents happen, way too frequently. Just look at the statistics:
- 25% of accidents occur at the loading dock (OSHA).
- For every accident, there are around 600 near-misses.
- Between 2015 and 2020, 33,000 employees missed work due to loading dock injuries.
- In 2018, 49 workers died from loading dock accidents.
This is all very preventable. And at Global Industrial, we want to do everything we can to educate employers and employees about basic safety procedures, and warehouse loading dock red flags. So, let’s start by defining the loading dock, and how it differs from the receiving dock.
Loading Dock vs Receiving Dock: Know The Difference.
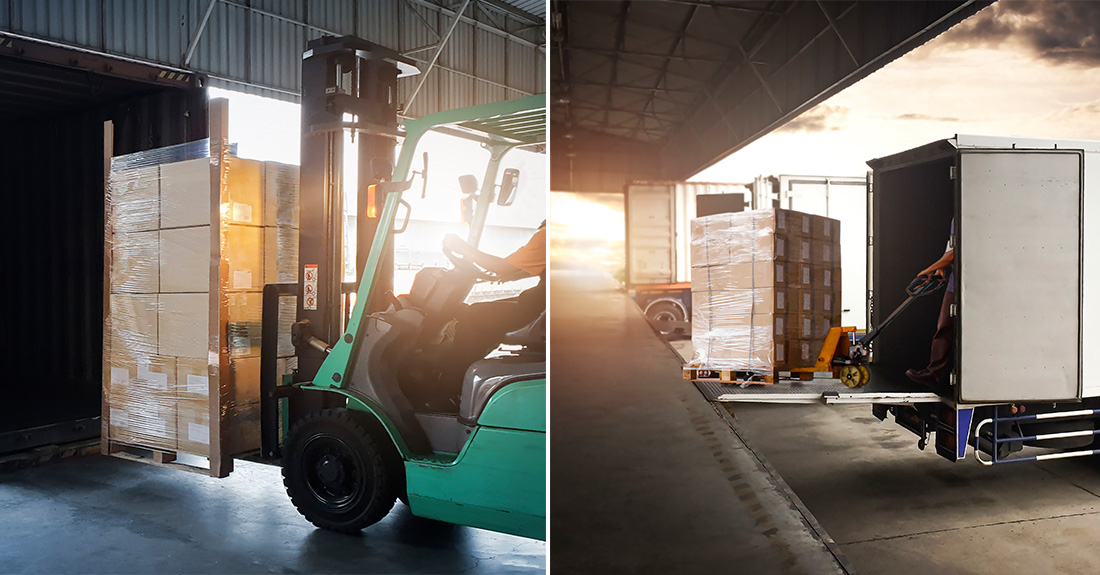
Sometimes referred to as the loading bay, the loading dock is the part of the warehouse that deals with goods being loaded and unloaded. However, it’s important to note that there is actually a different between a bay (the general area of the warehouse) and the dock itself, which is the actual platform that connects to a truck.
A receiving dock is a little different. This is the location where carriers deliver purchased goods and materials, and is the point at which the physical receipt of these goods/materials occurs. While both are crucial to the smooth running of your business, they are different entities. The loading dock is loading and unloading, the receiving dock is unloading only, and the goods involved can be different. Which brings us to the next key consideration of a loading dock:
From Indoors to Outdoors, and Vice Versa.
The loading dock is the doorway from your facility to the outside world. And of course, that presents several challenges on its own. While the inside operations are much easier to control throughout the year, including climate, air quality, and floor safety, it’s a lot more difficult to handle the extreme weather that can occur at many facilities. From blizzards, ice and hail, to sweltering temperatures and high humidity, these all have to be considered, and safety protocols for each need to be in place.
In winter, utilize dock shelters and dock seals to protect employees from harsh winter conditions, including falling ice, snow, hail, sleet and torrential rain. You should also create safe walkways, slip-resistant surfaces, and make sure the ramp and loading dock plate is free from water or snow at all times.
In summer, in addition to shelters and seals to protect from the sun and heat, ensure your facility has HVLS fans, high-speed doors, air curtains, and bug screens. Spraying water on trailers can also keep things a little cooler.
In both scenarios, you also need to take into account the goods and materials being loaded and unloaded. For instance, you may need specialized conveyor belts, and your logistics equipment may need to be modified for winter or summer use.
Get To Know Your Loading Dock
How well do you really know it, and the ins and outs of daily use? Well, it’s on you to understand the elements that create a safe and efficient loading dock environment. That means:
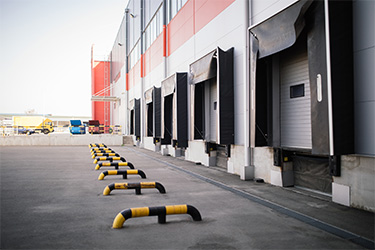
Elements that create a safe and efficient loading dock environment:
- Establishing a workflow design that’s intuitive for your employees, materials and the facility itself.
- Assessing your loading docks strengths and weaknesses. For instance, how many trucks will it need to service during the week? Are you ready to handle that workload, or does the loading dock need upgrades.
- Creating clear communication between managers and employees, and ensuring the right signage is placed in the correct areas for all to see.
Types of Loading Docks
There are usually four types of loading dock, and each will require a slightly different process, equipment, and dock safety measures.
- The Flush Dock. The most common loading dock has the simplest procedure. The truck driver backs the trailer up against the dock wall, the dock shelter creates a seal, and the loading/unloading can begin.
- The Enclosed Dock. Here, the trailer parks inside the building or a sheltered areas, and the loading and unloading takes place. However, these docks have disadvantages including high construction costs, taking up more space, and making it harder for workers to access supplies and equipment.
- The Saw-Tooth Dock. An innovative solution for docks that offer little room for truck-drivers to maneuver the trailer. Sawtooth docks have an opening at the front and a ramp that extends down from the dock to the ground. This allows forklifts to drive directly onto the dock, and provides a place for them to securely park when not in use.
- The Open Dock. The most unpopular design, and one that has the most safety issues. While it’s super easy to load and unload here, it’s a bad choice for easily-damaged goods. They also provide little-to-no protection from extreme weather conditions, and are susceptible to theft.
Regular Maintenance Keeps Everything Running Smoothly
It’s common sense that the busiest area in your warehouse is also the one that needs the most attention. Regular maintenance of the loading dock, and loading dock equipment and supplies, is the difference between hitting your targets and missing the mark. And of course, if you fall behind that costs time, money, and maybe even the loss of a client. So, check the following on a weekly schedule, and if you need dock door repair, and any other repairs, replacements, or upgrades, get to it sooner rather than later.
- Dock Bumpers
- This includes, but is not limited to: heavy duty loading dock bumpers; extended rubber fenders; steel-faced bumpers; specialty molded bumpers; replaceable bumper heads; high impact bumpers. For quality and reliability, you can’t go wrong with Ideal Warehouse bumpers.
- Containment Netting for dock door debris, and fire retardant netting.
- Swing Gates (available in multiple widths, heights, and optional safety alarms).
- The latest safety signage, signals, and fresh paint (including reflective paint colors).
- Guards and Railings
- Wheel Locks and Chokes
- Dock Levelers
- This includes: edge of dock levelers; mechanical and power pit mount dock levelers; portable steel platform docks; dock leveler accessories.
- Lighting for both indoor and outdoor usage.
- Seasonal equipment, such as tools to keep the outdoor dock area free from dangerous ice, snow and other hazardous surfaces.
The Importance of Dock Safety Training and Communication
Now that we’ve covered the loading dock environment, we need to talk about training. It cannot be stressed enough that even if you have the latest equipment, all the signs, barriers, nets, and non-slip floors, lack of safety education leads to serious accidents, and even deaths. So, it’s vital that you update your workers regularly on the latest safety policies, workflow design, regulations and equipment operation. And the following checklist is a great place to start:
- Use locking devices and wheel chocks with any vehicle at the dockAdd removable rails and dock barricades at all doors to minimize the risk of falls.
- Use padding on all sharp corners.
- Ensure all dock bumpers, dock seals, strip doors, and air curtains are properly installed and in perfect working order.
- Check the height of the slope from loading dock to vehicle; it should be 6% or less (and 5% for heavier loads)
- Use flexible bollards to protect both employees and equipment.
- Install conveyors specifically designed to help workers move materials in and out of the loading dock quickly and safely.
- Provide essential safety gear to all workers, which includes hard hats, gloves, reflective vests and steel-toed boots.
- Paint the dock with reflective yellow paint.
- Ensure proper lighting for inside and outside of the loading dock.
- Install the best bumper protection, which is a minimum of 4 inches tall.
- Choose the correct dock leveler(s) to even the height difference between the trailer and the dock. This ensures a seamless transition from the loading dock to the trailer, and vice versa.
- Add signage to the dock with safety messages. For example, “No climbing or jumping off dock” or “wheels chocks must be used.”
- Install dock signaling devices such as traffic lights.
- Supply the loading dock area with seasonal tools for different weather conditions, including equipment for snow and ice removal.
This is not a complete list of course. Every warehouse is different, and yours will no doubt have other specific areas that you may need to address. Remember, loading docks are dangerous areas, especially if you don’t have the latest safety regulations in place. The most common accidents on loading docks are easily preventable and include:
• Slips and falls.
• Injuries from lifting, pulling, pushing, and overreaching.
• Forklift and material handling.
By paying just a little extra attention to safety procedures, and having the most up-to-date conveyors, forklifts, barriers and other loading dock equipment, you can help reduce these unnecessary industrial accidents. And if you need any help with warehouse safety solutions, including the latest safety equipment on the market, our experts are here to help.
The information contained in this article is for informational, educational, and promotional purposes only and is based on information available as of the initial date of publication. It is the reader’s responsibility to ensure compliance with all applicable laws, rules, codes and regulations. If there is any question or doubt in regard to any element contained in this article, please consult a licensed professional. Under no circumstances will Global Industrial® be liable for any loss or damage caused by your reliance on this article.